For oil-fired gas boilers, improving thermal efficiency can effectively save fuel and achieve the purpose of energy-saving and money-saving. So what are the methods and techniques that can improve the thermal efficiency of oil-fired and gas-fired boilers? Let Zhengzhou Fangkuai Boiler Factory come to answer you for free.
1. Adopt flue gas waste heat recovery technology to reduce flue gas loss. The main factor that affects the heat loss of exhaust gas is the exhaust gas temperature. The higher the exhaust temperature, the greater the exhaust heat loss. At present, most of the newly built boilers are equipped with flue gas waste heat recovery devices when they leave the factory, such as economizers, semi-condensing or fully condensing flue gas waste heat recovery devices. These measures can effectively reduce the exhaust gas temperature and improve the thermal efficiency of the boiler.
2. When the excess air coefficient is too high, it is equivalent to inhaling excess cold air into the furnace. This part of the excess cold air does not participate in the combustion but is discharged in vain after being heated, and the heat loss of exhaust smoke increases; The cold air continues to increase. If the temperature exceeds a certain limit, the furnace temperature will decrease, which will also cause the loss of incomplete combustion to increase. When the excess air coefficient is too low, the fuel cannot get enough oxygen and cannot be completely combusted, resulting in increased incomplete combustion loss. Long-term severe incomplete combustion will result in carbon in the heated area of the boiler, which will affect the heat exchange efficiency and continue to increase the loss of flue gas. Therefore, reasonable control of the air-fuel ratio and minimized exhaust heat loss q2 and incomplete combustion loss q3 is another key point for improving the thermal efficiency of the boiler.
3. Strictly control boiler water quality and scientifically control scale. The thermal conductivity of scale is very low, so once the heating surface is scaled, due to the increase of thermal resistance, the boiler exhaust temperature will rise, and the exhaust heat loss will increase. The test data shows that a 1mm scale on the heating surface of the boiler will increase the heat loss of exhaust flue gas by about 2% to 4%. The thicker the scale on the heating surface of the boiler and the greater the thermal resistance, the more the boiler thermal efficiency will drop. Boiler fouling not only reduces the thermal efficiency of the boiler, but also increases the wall temperature of the heating surface of the boiler, causing damage to the heating surface, and even a boiler explosion accident. Therefore, the use of high-quality soft water treatment devices and strictly follow the process to operate the boiler feed water softening treatment device to control the boiler feed water quality can delay the formation of scale. At the same time, it is also very important to conduct real-time control of boiler scale, grasp the status of boiler scale, and clean up when necessary.
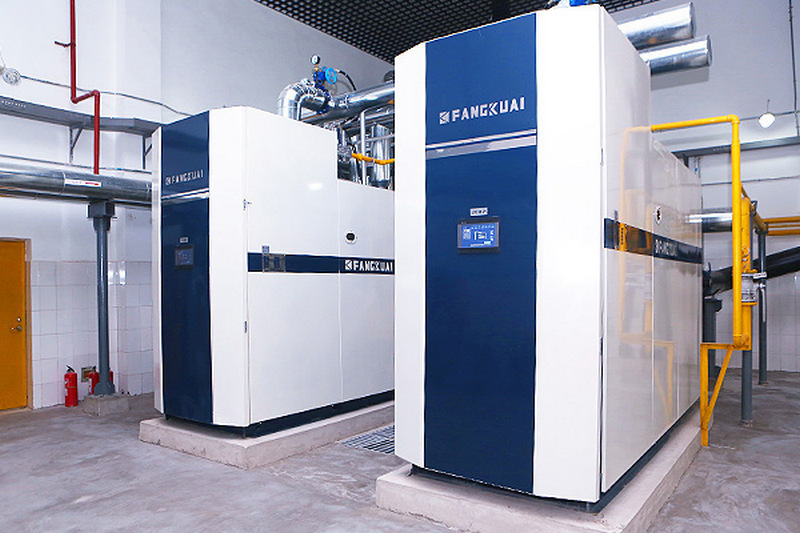